
BLOG
How to Choose the Right Hydraulic Chuck for Your Machining Needs
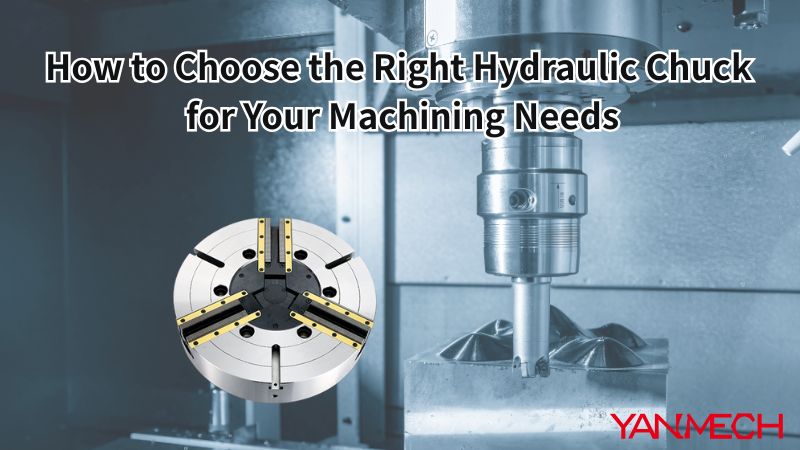
In today's precision-driven manufacturing world, choosing the right hydraulic chuck can significantly impact machining accuracy, tool life, and overall production efficiency. Whether you're in aerospace, automotive, mold manufacturing, or electronics, a well-matched hydraulic chuck ensures repeatability and stability in your CNC machining processes.
With decades of hands-on experience in precision workholding, YANMECH Industrial Co., Ltd. has seen how the right hydraulic chuck can make a measurable difference in machining outcomes. This article outlines the key considerations we believe every manufacturer should keep in mind when selecting a hydraulic chuck—ensuring both performance and long-term reliability.
1. Understand Your Machining Application
Every machining setup is different, and the first step to making the right chuck choice is knowing exactly what your operation demands.
Ask yourself:
- Are you machining small precision parts or heavy components?
- Is surface finish critical to your application?
- Will the chuck be used in high-speed machining or interrupted cutting?
- Do you require quick tool changes or extended production runs?
For example, a mold and die manufacturer may need a chuck with ultra-low runout for contour finishing, while an automotive supplier may prioritize rigidity and clamping force for mass production.
Understanding the nature of your production environment will help you match the chuck’s features to your performance goals.
2. Check Clamping Range and Bore Size
Hydraulic chucks typically use a clamping sleeve to secure the cutting tool, allowing for quick and secure tool changes. However, choosing the wrong bore size or misusing sleeves can lead to instability and vibration.
Consider:
- The tool shank type (straight, tapered, Weldon)
- Shank diameter and tolerance class (e.g., h6 or h7)
- The possibility of using reduction sleeves or solid collets
If you switch tools frequently, opting for a standard bore with multiple sleeve options will increase flexibility and reduce downtime.
3. Evaluate Runout and Clamping Force
Precision is a defining advantage of hydraulic chucks. Typical total indicator runout (TIR) is less than 0.003 mm. This level of accuracy helps:
- Maintain consistent cutting paths
- Reduce spindle vibration
- Improve tool life and surface quality
However, precision must be balanced with grip. A chuck with too little clamping force will allow micro-movements during cutting, affecting part accuracy. Ensure your chuck can handle the torque requirements of your machining strategy.
4. Select the Right Shank Interface
Your chuck must fit your machine's spindle system securely. The choice of shank interface affects not just compatibility, but also balance, tool change time, and overall machining dynamics.
Common types include:
- BT (MAS 403): Popular in Asia; strong clamping and widely used
- HSK (DIN 69893): Hollow shank taper; ideal for high-speed and precision
- CAT (ANSI B5.50): Common in North America
- PSC (Capto): Modular, suited for multi-tasking machines
Consider using dynamically balanced chucks if your application exceeds 10,000 rpm, especially in aerospace or medical part production.
5. Consider Coolant-Through Capabilities
Coolant delivery is crucial in today's high-speed and deep-hole machining environments. Choosing a hydraulic chuck with internal coolant-through capability can:
- Extend tool life
- Improve chip evacuation
- Reduce thermal deformation
- Support high-pressure systems (often over 70 bar)
Some chucks feature center-coolant systems, while others use peripheral coolant flow. Matching the coolant path to your tool and machine helps maximize cutting efficiency.
6. Look for Additional Features
Modern hydraulic chucks come with enhancements that improve usability and versatility, including:
- Anti-vibration design: Reduces chatter in thin-wall or long-reach machining.
- Slim nose profiles: Ideal for reaching tight cavities or 5-axis applications.
- Quick-change sleeves: Speeds up tool changeover and increases productivity.
- Anti-pullout mechanisms: Critical for aerospace or hard-metal cutting where tool security is paramount.
These features add to the chuck's value over time by enabling broader usage and minimizing machine downtime.
Common Mistakes to Avoid When Choosing a Hydraulic Chuck
Even experienced buyers may overlook a few critical aspects:
- Ignoring balance class: Unbalanced chucks can cause tool vibration and premature spindle wear.
- Using incompatible sleeves: Poor sleeve fit can reduce clamping accuracy.
- Skipping coolant compatibility check: This leads to leaks or coolant starvation.
- Overestimating grip force: Not all hydraulic chucks are designed for heavy-duty roughing.
Working with a knowledgeable supplier helps eliminate these pitfalls.
Why Choose YANMECH Hydraulic Chucks
- Exceptional Rigidity for Stable Machining
Constructed with high-strength materials and an optimized structural design, YANMECH's hydraulic chucks offer outstanding rigidity, ensuring stability during heavy-duty cutting and high-load operations.
- Precise Clamping for Perfect Accuracy
Advanced manufacturing processes and strict quality control guarantee repeatable jaw positioning, enabling micron-level machining precision. Stable clamping force prevents workpiece displacement or deformation during machining.
- High-Performance Protection for Extended Service Life
The precision sealing design effectively prevents the intrusion of cutting fluids, chips, and other contaminants, protecting internal components and extending the chuck's service life. This reduces maintenance frequency and lowers production costs.
- Versatile Application and Multi-Process Support
Compatible with various precision machining equipment, including CNC lathes, multi-tasking machines, and grinding machines. Capable of handling short workpieces, heavy-duty cutting, and high-precision machining requirements.
- Customizable Solutions
YANMECH offers tailored solutions to meet specific customer requirements, ensuring the best fit for your equipment and machining needs.
Conclusion: Choose Precision, Choose the Right Partner
Selecting the right hydraulic chuck requires careful consideration of your machining environment, performance goals, and equipment compatibility. A high-quality chuck not only improves clamping accuracy but also extends tool life, enhances surface finish, and boosts overall productivity.
If you're looking for reliable, high-performance hydraulic chucks and customized workholding solutions, YANMECH Industrial Co., Ltd. is here to help. With over 30 years of experience and a strong foundation in CNC workholding systems, we support clients across aerospace, semiconductor, and traditional industries. Contact us today to find the right hydraulic chuck for your application.